N-butane Isomerization ISOMALK-3
Eco-friendly technology for normal butane isomerization to isobutane to yield high-purity feedstock for chemical synthesis, production of alkylate, ETBE, MTBE, and butyl rubber
There is a growing demand for high-octane alkylate, isobutylene, ETBE, MTBE, and butyl rubber on the global market. The feedstock in the production process of these products is high-purity isobutane.
Isobutane production by n-butane isomerization according to the innovative technology Isomalk-3 over SI-3 catalyst is the most advanced, efficient, and cost-effective method to provide feedstock for these processes.
Until recently, the most common commercial method of normal butane isomerization was the process based on chlorinated catalyst.
Having a high degree of activity and selectivity, chlorinated catalysts also have a number of disadvantages: equipment corrosion, frequent replacement of expensive catalysts, and toxic wastes. All this leads to an increase in CAPEX, OPEX, and hence to a high production cost.
The only alternative method for isobutane production on a commercial scale is to use the oxide catalyst SI-3 not containing chlorine as an active component.
SI-3 catalyst and the technology of its use were developed in SIE Neftehim’s scientific research laboratory, and thereafter they have been successfully applied at a number of industrial enterprises. The butane isomerization technology Isomalk-3 constitutes a follow-up to the series of IsomalkTM technologies over SITM series catalysts.
Isomalk-3 technology advantages
As compared to technologies over chlorinated catalysts, Isomalk-3 technology has the following advantages:
- Isomalk-3 technology does not involve aggressive reagent supply; there is no process equipment corrosion; no process wastes and effluents that require disposal. The product does not contain chlorine and sulfur micro impurities.
- Minimum OPEX due to the absence of aggressive reagents and need to treat product and off-gas to remove chlorine impurities; the long service cycle and service life of adsorbents, the minimization of shutdowns during catalyst operation.
- High robustness of the catalytic system. Temporary increase in feed impurities content does not lead to irretrievable loss of the catalyst activity.
- Long service life of SI-3 catalyst - more than 10 years. The catalyst does not require any reloading or additional loading during the whole service life.
- Tolerance to catalytic poisons. No special aftertreatment of feed to remove moisture, sulfur, and nitrogen micro impurities is required. Temporary changes in feed quality do not lead to irretrievable loss of activity, unlike with chlorinated catalysts.
Upon conversion of existing n-butane isomerization unit operating over chlorinated catalyst to Isomalk-3 technology, OPEX will be reduced by approximately 20%.
Ease of introduction
Isomalk-3 technology is universal for any new or existing plant:
Option 1. Replacement of chlorinated catalyst in existing unit with SI-3 catalyst without revamp. In this case, idle equipment for chlorinated system will be disengaged, and unit OPEX will decrease.
Option 2. Engineering design and construction of a grass-root unit using all the technology advantages. Optimal construction period is 2 years from engineering design start date.
To evaluate the effect of the technology introduction, we are ready to make a free technical and economic evaluation for your enterprise. For this, please contact us through feedback form.
How does Isomalk-3 operate?
Unit feed is butane fraction. Isomerization reaction proceeds over SI-3 catalyst in the presence of hydrogen.
Isomalk-3 process includes the following stages:
1) Separation into iso- and n-butane fractions, separation of C5+ hydrocarbons in deisobutanizer section
2) Feed and hydrogen treatment in dryers to remove undesirable impurities
3) Butane fraction isomerization reactions over SI-3 catalyst in one or several reactors in series
4) Separation of dissolved hydrogen and light hydrocarbons (C1-C3) from product in stabilization column section (C-2) and sending stabilized product to fractionation column section (C-1) to produce high-purity isobutane
Unconverted n-butane is recycled back to isomerization reactor section, thereby ensuring maximum conversion of n-butane to isobutane.
Isomalk-3 technology catalytic system
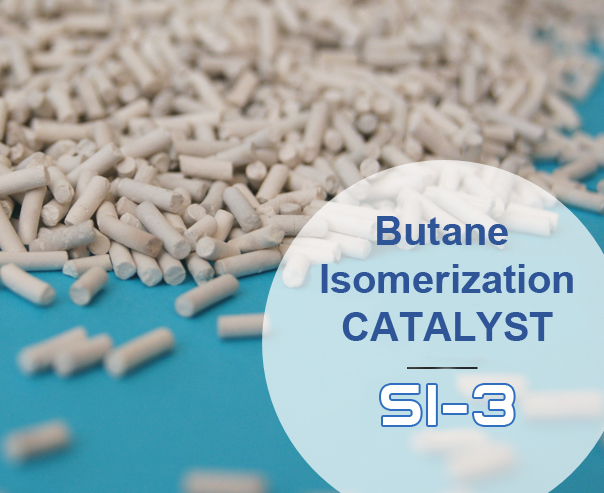
SI-3 catalyst advantages over chlorinated catalysts for butane isomerization:
• Long service life of the catalyst – not less than 10 years
• Possibility to restore catalyst activity
• Chlorine-containing compound supply is not required
• No acid gas caustic treatment
• No wastes that require special handling
• No chlorine and sulfur impurities in product
The combination of the capabilities provided by the modern research laboratory of SIE Neftehim, the availability of pilot units, and own catalyst manufacturing plant allows us to improve the produced catalysts with each new batch.
Each batch of catalysts produced by SIE Neftehim undergoes double quality control and 24/7 pilot tests immediately before shipment to Customer.
SI-3 catalyst quality has been confirmed by its successful long-term operation at commercial units.
Commercial use of Isomalk-3 technology
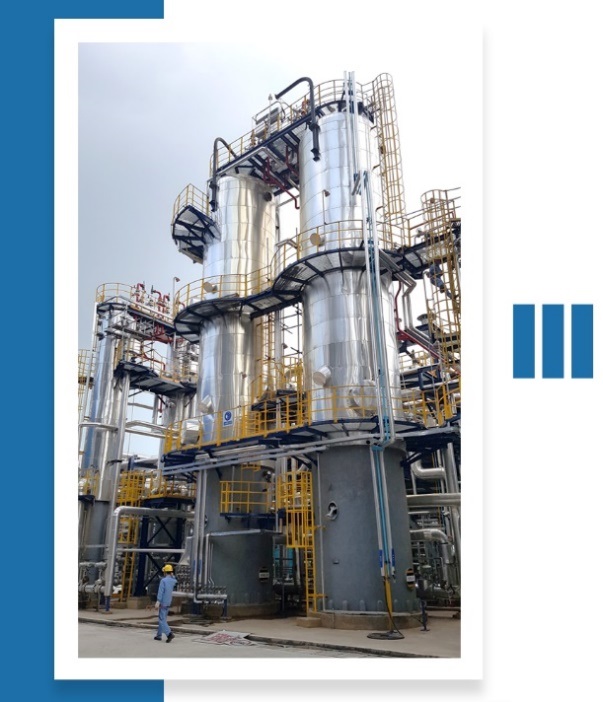
The world's first n-butane isomerization unit according to Isomalk-3 technology operating over non-chlorinated oxide catalyst was commissioned in 2016 in China and is a part of MTBE production complex licensed by Lummus.
The nominal feed (butane fraction) capacity of the unit is 200 KTA.
The project customer is Shandong Sincier Petrochemical Co., Ltd (China).
The company resorted to Isomalk-3 technology, as the used dehydrogenation catalyst was very sensitive to chlorine impurities in feed and the use of chlorinated catalyst system involved high risks. The breakthrough of chlorine in isobutane fraction could lead to the shutdown of the entire complex. Since SI-3 catalyst does not require chlorine supply to feed, the choice was made in favor of Isomalk-3 technology. The project was successfully implemented and, immediately after its start-up, attracted interest of other oil refining companies.
In 2017-2018, in China another two small-scale units Isomalk-3 with 30 KTA feed capacity each were built and started up.
Later, in 2019, the largest unit Isomalk-3 was built and commissioned at Sinopec Jinling Petrochemical refinery (Nanjing, China), owned by the national oil refining corporation of China.
To process butane in large volumes, the efficient and reliable technology was required. In this case, the main problems of stability, environmental friendliness, and robustness of the process were solved.
The unit capacity in terms of unit reactor section feed is 480 KTA.
Isomalk-3 unit construction: key stages
The whole process from idea to operating plant can be divided into the following main stages:
• Inspecting an existing plant
• Isomalk-3 technology implementation feasibility study
• Making a decision on construction and kick-off meeting with all project participants
• Development of Basic Engineering Design – it contains all the fundamental calculations and mandatory technology requirements
• Detailed Engineering Design - by a specialized engineering company involved by SIE Neftehim or a customer/investor
• Ordering the equipment
• Construction
• Personnel training in unit operation procedures and skills
• Catalyst supply
• Pre-commissioning
• Start of product manufacturing
Experienced experts of SIE Neftehim give project support at all stages as well as monitor the current operation of a unit and, if necessary, provide recommendations for performance improvement.
SIE Neftehim always promptly provides consulting and technical assistance in solving current production tasks.
If you are interested in effective solutions in isomerization field and ready to discuss a prospective project, you can contact us through feedback form. Please provide general information about your company and contact details for communication. Our experts will certainly reply to you.
Additional materials to the article:
News of SIE Neftehim: Chinese Sinopec has started up one of the most high-capacity isobutane production unit |
|
«High performance production solutions for modern motor gasoline»Pipeline Oil & Gas Egypt, February 2020 (issue on EGYPS-2020 exhibition), №2-2020 |
|
ISOMALK-3: new technology of n-butane isomerizationThe special issue of industrial, scientific, technical and economical development magazine «Technopolis XXI» №33 (2016, p. 22) |
|
Full list of SIE Neftehim publications in print media
«Isomalk» and «SI» are registered trademarks. All rights reserved by SIE Neftehim, LLC exclusively.